How Packaging Equipment Repair Services Help Prevent Costly Downtime
How Packaging Equipment Repair Services Help Prevent Costly Downtime
Blog Article
Explore Why You Need Trustworthy Packaging Tools Repair Provider for Ideal Production
In the affordable landscape of production, reliable product packaging tools fixing solutions play a necessary role. Timely interventions can drastically minimize devices downtime and enhance manufacturing efficiency. Numerous services forget the value of attending to mechanical failings immediately. This oversight can cause significant operational difficulties. Recognizing the nuances of repair solutions and their ramifications on manufacturing might be crucial for firms going for continual success. What elements should services think about to assure they choose the appropriate fixing solution?
The Value of Timely Services in Manufacturing
Although equipment breakdowns are commonly unavoidable, the value of prompt repair work in manufacturing can not be overemphasized. When tools malfunctions, the entire assembly line can be interrupted, leading to expensive hold-ups and lowered productivity. Manufacturers depend on their machinery to operate efficiently; as a result, punctual repair work are necessary to decrease downtime.Delays in attending to devices issues can escalate into larger issues, influencing item high quality and functional effectiveness. Prompt repair work not just recover performance yet also prolong the lifespan of the equipment, eventually minimizing lasting prices linked with substitutes. Furthermore, preserving tools in ideal problem supports office safety, as malfunctioning tools can pose dangers to employees.In the affordable landscape of production, focusing on timely fixings is crucial for sustaining operations and meeting customer needs. Spending in trustworthy fixing services is a critical move for producers aiming to improve efficiency and keep high production requirements.
Usual Concerns With Product Packaging Equipment
Packaging devices typically experiences a variety of usual issues that can impede production efficiency. One widespread problem is mechanical failing, which may emerge from worn components or insufficient maintenance. This can lead to breakdowns that interfere with the product packaging process. An additional typical problem is imbalance, where product packaging machinery stops working to function appropriately due to inappropriate setup, leading to item damage or waste. On top of that, controls and sensing units can malfunction, resulting in incorrect dimensions and operational errors.Over time, wear and tear can also cause conveyor belts to slide or jam, influencing the flow of materials. Software program problems in automated systems might result in hold-ups or wrong packaging arrangements. Routine surveillance and prompt repair work can reduce these issues, guaranteeing smoother operations. Dealing with these usual concerns proactively is necessary for preserving perfect efficiency in product packaging operations.
Exactly How Tools Downtime Impacts Your Organization
Exactly how does devices downtime influence a service's overall productivity and earnings? Devices downtime can considerably prevent a firm's procedures, leading to lowered production outcome and postponed distribution times. When machinery stops working, staff members might be forced to stand still, wasting useful labor hours and impacting workforce morale. This interruption can waterfall via the supply chain, causing unmet customer needs and prospective loss of contracts.Moreover, the economic effects of tools downtime extend beyond immediate losses. Firms might experience raised functional costs because of overtime payments or expedited shipping to satisfy orders. In extremely open markets, prolonged downtime can tarnish a company's online reputation, driving consumers towards more trusted rivals. Inevitably, the combination of lost productivity, boosted costs, and possible reputational damages emphasizes the critical requirement for prompt and efficient packaging tools repair solutions to preserve peak operations and assure continual profitability.
Cost-Benefit Analysis of Expert Repair Solutions
Examining the financial effects of equipment downtime exposes the importance of expert repair solutions. Hold-ups in production can result in considerable profits losses, influencing the general earnings of an organization. Investing in expert repair work services not only reduces downtime however additionally assures that equipment operates at peak efficiency.While the preliminary expense of working with proficient service technicians may seem high, the long-lasting benefits typically surpass these costs. Trustworthy repair services expand the life expectancy of equipment, decreasing the requirement for costly substitutes. In addition, specialist servicing can prevent unanticipated failures that interfere with procedures and incur more costs (Packaging Equipment Repair Services).Companies that prioritize professional fixing solutions usually experience improved product top quality and consistency, boosting client complete satisfaction. Inevitably, a well-executed cost-benefit evaluation highlights that the investment in specialist repair work solutions is not simply an expense, however a strategic approach to securing manufacturing performance and economic security in the competitive packaging market
Selecting the Right Fixing Company
When choosing a repair work solution supplier, what key factors should organizations think about to ensure ideal results? First, the service provider's experience and knowledge in servicing particular product packaging devices is basic. A firm with a tested record in the market can guarantee that repair services are performed effectively and effectively. Additionally, evaluating the supplier's qualifications and training can suggest their dedication to keeping high standards.Second, responsiveness and accessibility play a vital role. A reputable repair work solution ought to offer quick reaction times and adaptable organizing to minimize downtime. Third, companies ought to analyze consumer evaluations and reviews, as these can give understandings into the supplier's dependability and top quality of service.Finally, transparent prices and service warranty alternatives are critical. A trustworthy supplier needs to stand and supply clear estimates behind their job, assuring that companies receive value for their financial investment. By taking into consideration these elements, firms can choose a repair service that satisfies their certain demands.
Preventative Maintenance to Extend Equipment Lifespan
Preventative upkeep plays an important function in extending the lifespan of product packaging devices. Carrying out regular evaluation schedules, lubrication, calibration, and strategic element replacement can significantly reduce downtime and repair work expenses. By prioritizing these practices, companies can enhance functional effectiveness and guarantee trustworthy efficiency.
Normal Evaluation Schedules
Regular inspection schedules play an important duty in the durability of product packaging devices, ensuring excellent performance and reducing the chance of unanticipated failures. By adhering to a systematic evaluation regimen, services can recognize deterioration, resolve prospective issues, and enhance devices capability. These evaluations typically include checking essential elements, assessing performance metrics, and examining overall equipment condition. Normal evaluations assist develop a standard for efficiency, making it much easier to identify variances that might indicate a trouble. Packaging Equipment Repair Services. Furthermore, set up examinations can assist in better preparation for upkeep and repair work, minimizing downtime and enhancing efficiency. Ultimately, implementing normal inspection timetables adds to a positive maintenance strategy that advertises operational efficiency and expands the lifespan of packaging tools
Lubrication and Calibration
Effective upkeep regimens, such as routine assessments, normally result in the requirement for lubrication and calibration to assure peak efficiency of product packaging equipment. Lubrication decreases friction, decreasing deterioration on moving components, which can substantially prolong the lifespan of equipment. Regularly used lubricating substance helps preserve operational effectiveness, protecting against overheating and prospective malfunctions. Calibration, on the various other hand, warranties that tools runs within defined specifications, therefore boosting precision and consistency in manufacturing. Failure to correctly adjust or oil can cause expensive downtimes and repair work. Subsequently, including these techniques into a preventative maintenance method fosters integrity, increases performance, and eventually supports a steady production setting. Focusing on lubrication and calibration is crucial for preserving ideal tools performance.
Element Substitute Approaches
An aggressive method to component substitute plays a necessary function in prolonging the lifespan of product packaging tools. Routinely examining the condition of crucial parts, such as belts, electric motors, and seals, makes it possible for drivers to determine wear and potential failings before they endanger manufacturing. Implementing an organized routine for element substitute, based on manufacturer recommendations and usage patterns, can greatly reduce downtime and repair work costs. In addition, making use of high-grade replacement components warranties compatibility and efficiency, better boosting operational efficiency. Training employees to identify very early signs of wear and assisting in timely substitutes not just stops unforeseen malfunctions however likewise promotes a society of upkeep understanding. Ultimately, efficient element substitute techniques add to sustained efficiency and dependability in product packaging procedures.
Case Researches: Success Stories From Reliable Fixes
Taking a look at real-world examples exposes the substantial effect of efficient product packaging devices fixings on operational productivity. One noteworthy case included a drink company that dealt with frequent device failures, causing substantial manufacturing delays. By partnering with a dependable repair work service, they implemented a preventative maintenance plan that lowered devices blog downtime by 40%. In my blog an additional circumstances, a treat supplier experienced bottlenecks due to malfunctioning securing devices. After purchasing specialized fixing services, they enhanced device efficiency, leading to a 30% boost in output.These instances show that timely and effective repair services not only bring back functionality but also add to enhanced manufacturing rates. By focusing on reliable fixing solutions, business can reduce functional interruptions and cultivate an extra effective atmosphere. Such success stories highlight the value of spending in dependable packaging equipment fixing solutions to secure lasting operational efficiency.
Regularly Asked Questions
What Credentials Should I Search For in Fixing Technicians?
When taking into consideration fixing service technicians, one should focus on certifications in pertinent machinery, experience with particular devices, analytical abilities, and a solid performance history of integrity (Packaging Equipment Repair Services). Good interaction and adherence to safety requirements are likewise vital credentials to seek
How Can I Identify When My Devices Requirements Repair Works?
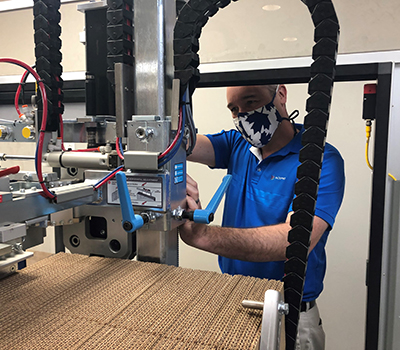
What Sorts Of Product Packaging Tools Call For Specialized Repair Providers?

Exist Service Warranties for Repair Services on Product Packaging Equipment?
Service warranties for repair work solutions on packaging equipment differ by supplier. Usually, reputable companies provide service warranties to ensure high quality and dependability, covering components and labor for a given period, thereby boosting customer self-confidence in their solutions.
Just how Do I Arrange Emergency Situation Repair Work Services?
To set up emergency repair service solutions, one commonly get in touches with the provider directly via phone or their website. Trigger interaction assurances a swift response, enabling timely resolution of tools concerns and minimizing production disturbances. In the affordable landscape of manufacturing, trustworthy packaging devices repair work solutions play a necessary duty. Additionally, preserving devices in perfect condition sustains workplace security, as defective tools can posture risks to employees.In the affordable landscape of production, focusing on punctual fixings is look at here vital for sustaining procedures and meeting consumer needs. After spending in specialized repair work services, they enhanced device performance, resulting in a 30% increase in output.These cases illustrate that prompt and reliable repair services not just bring back performance however also contribute to enhanced manufacturing rates. Certain types of product packaging devices, such as vacuum sealants, labeling machines, and automated conveyors, commonly need customized fixing solutions. Warranties for repair services on product packaging devices differ by copyright.
Report this page